Fabric making machines, particularly those used for non-woven fabric production, are designed to handle variations in web formation and bonding to ensure consistent product quality.
Here’s how they typically address these variations:
- Adjustable Process Parameters: Fabric making machines feature adjustable process parameters such as line speed, air pressure, temperature, and tension control. Operators can fine-tune these parameters to accommodate variations in raw material properties, web formation characteristics, and bonding requirements.
- Multiple Web Formation Methods: Fabric making machines may offer flexibility in web formation methods, including spunbond, meltblown, needle punching, hydroentanglement, and chemical bonding. Different methods are suitable for different applications and can be selected based on desired fabric properties and performance.
- Variable Web Width: Some fabric making machines allow for variable web width, enabling operators to adjust the width of the fabric according to production requirements. This feature helps optimize material usage and accommodate variations in web formation without compromising efficiency.
- Inline Monitoring and Control Systems: Advanced fabric making machines are equipped with inline monitoring and control systems that continuously monitor key parameters such as web thickness, basis weight, and uniformity. These systems provide real-time feedback to adjust process parameters and ensure consistent web formation and bonding.
- Uniform Distribution of Fibers or Particles: Fabric making machines are designed to ensure uniform distribution of fibers, particles, fabric making machine or other raw materials across the web during formation. Proper distribution is essential for achieving consistent bonding and mechanical properties throughout the fabric.
- Bonding Methods and Technologies: Various bonding methods and technologies are available in fabric making machines, including thermal bonding, mechanical bonding (needle punching, hydroentanglement), chemical bonding (adhesive bonding), and ultrasonic bonding. Operators can select the most suitable bonding method based on the specific requirements of the fabric.
- Pre-treatment and Conditioning: Pre-treatment processes such as fiber opening, blending, and carding may be employed to prepare raw materials for web formation and bonding. Conditioning techniques such as heating, humidification, or chemical treatment can further optimize material properties for enhanced bonding.
- Adaptive Control Algorithms: Fabric making machines may utilize adaptive control algorithms that adjust process parameters dynamically based on real-time feedback from sensors and quality inspection systems. These algorithms optimize web formation and bonding to meet target specifications and minimize material waste.
By incorporating these features and practices, fabric making machines can effectively handle variations in web formation and bonding, ensuring the production of high-quality fabrics with consistent properties and performance.
What measures are in place to ensure the hygiene and cleanliness of produced materials?
Ensuring the hygiene and cleanliness of produced materials is essential, especially in industries such as medical, food, and hygiene products manufacturing.
Fabric making machines implement several measures to maintain hygiene and cleanliness standards:
- Cleanroom Environments: Fabric making machines used in industries with strict cleanliness requirements, such as medical or food production, may operate in cleanroom environments. Cleanrooms are controlled environments with regulated air filtration, temperature, humidity, and particle levels to minimize contamination.
- Material Handling Practices: Fabric making machines incorporate hygienic material handling practices to prevent contamination. This includes using enclosed conveyors, chutes, and transfer systems to minimize exposure of raw materials to external contaminants during transportation and loading.
- Sanitary Design: Fabric making machines are designed with sanitary principles in mind to facilitate easy cleaning and maintenance. Smooth surfaces, rounded corners, and minimal crevices reduce the risk of microbial growth and make cleaning more effective.
- Removable and Washable Components: Fabric making machines feature removable and washable components, such as conveyor belts, guide rails, and tooling, that come into direct contact with the product. These components can be easily detached for cleaning and sterilization between production runs.
- Cleaning-in-Place (CIP) Systems: Some fabric making machines are equipped with CIP systems that automate the cleaning process. non woven machines CIP systems circulate cleaning solutions, such as detergents or sanitizers, through the machine’s internal components to remove residues and contaminants without disassembly.
- Sanitary Seals and Gaskets: Fabric making machines use sanitary-grade seals and gaskets to prevent leakage and contamination. These seals are made from materials that resist degradation and bacterial growth and are designed to be easily cleaned and sanitized.
- Air Filtration and Ventilation: Fabric making machines incorporate air filtration and ventilation systems to maintain clean air quality within the production area. HEPA filters and air scrubbers remove airborne particles and contaminants, reducing the risk of product contamination.
- Operator Hygiene Practices: Operators working with fabric making machines adhere to strict hygiene practices, including wearing clean uniforms, hairnets, gloves, and other personal protective equipment (PPE). Handwashing and sanitization protocols are enforced to prevent cross-contamination.
- Quality Assurance and Testing: Fabric making machines undergo regular quality assurance testing to ensure compliance with hygiene and cleanliness standards. Product samples are analyzed for microbial contamination, particle counts, and other indicators of cleanliness to verify product quality.
By implementing these measures, fabric making machines can maintain high standards of hygiene and cleanliness, ensuring the production of safe and sanitary materials for various applications.
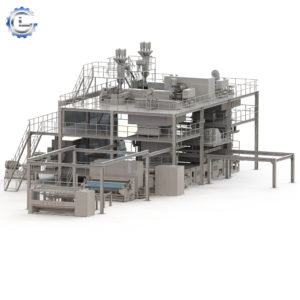