China Fiber Laser Cutting Machine suppliers typically handle customization requests through a structured process aimed at meeting the specific needs and preferences of their clients.
Here’s how they typically manage customization requests:
- Initial Consultation: The supplier begins by conducting a thorough consultation with the client to understand their specific requirements, including desired features, dimensions, materials, and any other customization preferences.
- Technical Assessment: After gathering the client’s requirements, the supplier’s technical team assesses the feasibility of the customization request. They evaluate factors such as the machine’s design, capabilities, and compatibility with the requested modifications.
- Proposal Submission: Based on the assessment, the supplier prepares a detailed proposal outlining the scope of customization, including specifications, timelines, and costs involved. This proposal serves as a basis for further discussions and agreement between the supplier and the client.
- Collaborative Design Process: If the client approves the proposal, the supplier engages in a collaborative design process, involving iterative discussions and feedback exchanges to finalize the customized solution. This may include providing design mock-ups, CAD drawings, or prototypes for client review and approval.
- Testing and Validation: Once the design is finalized, the supplier conducts rigorous testing and validation procedures to ensure that the customized machine meets the client’s specifications and quality standards. This may involve prototype testing, performance evaluations, and quality assurance checks.
- Production and Assembly: Upon successful validation, the supplier proceeds with the production and assembly of the customized machine. China Fiber Laser Cutting Machine suppliers They utilize advanced manufacturing techniques and technologies to fabricate components and integrate the necessary modifications seamlessly.
- Quality Control: Throughout the production process, the supplier implements strict quality control measures to monitor and verify the quality of the customized machine. This includes inspections at various stages of production to identify and address any deviations from the client’s specifications.
- Final Acceptance and Delivery: Once the customized machine is completed, the supplier conducts a final acceptance test to ensure that it meets all agreed-upon requirements. Upon client approval, the machine is prepared for shipment and delivered to the client’s location, along with any necessary documentation and support materials.
- After-Sales Support: After delivery, the supplier provides comprehensive after-sales support to assist the client with installation, training, maintenance, and troubleshooting. They remain responsive to any additional requests or feedback from the client, ensuring a positive post-purchase experience.
Overall, China Fiber Laser Cutting Machine suppliers prioritize effective communication, technical expertise, and quality assurance throughout the customization process to deliver tailored solutions that meet their clients’ unique needs and expectations.
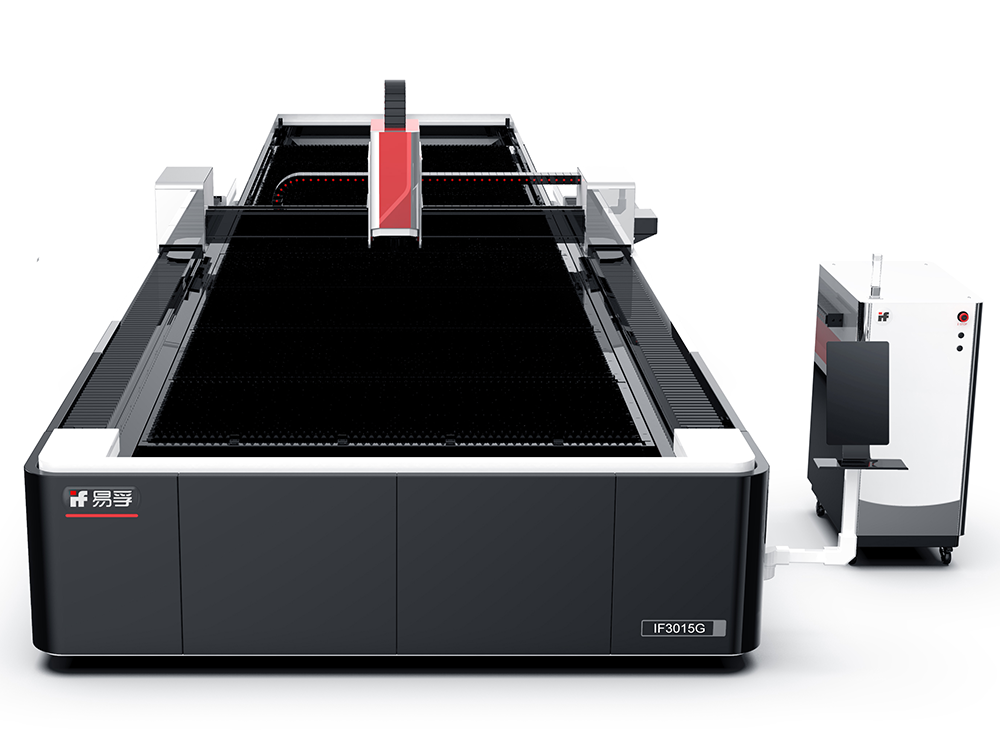