The demolding process in a concrete block making machine is crucial to ensure that the freshly formed blocks are released from the molds without being damaged.
Here’s how the machine typically manages this process:
- Release Agents: Before the concrete mixture is poured into the molds, release agents may be applied to the inner surfaces of the molds. These agents help prevent the concrete from sticking to the mold walls, making it easier to demold the blocks without causing damage.
- Vibration: Many concrete block making machines incorporate vibration systems that are activated during the demolding process. cinder block machine The vibrations help loosen the freshly formed blocks from the molds, reducing friction and facilitating smooth release.
- Hydraulic Systems: Hydraulic systems are commonly used to actuate the mold clamps or mold frames, which hold the molds in place during the block formation process. Once the blocks are ready to be demolded, hydraulic cylinders or actuators are engaged to release the molds, allowing the blocks to be removed gently.
- Precision Mold Design: The molds themselves are designed with precision to ensure that the blocks can be easily demolded without sticking or getting damaged. Smooth inner surfaces, rounded edges, and proper venting channels are incorporated into the mold design to facilitate smooth demolding.
- Optimized Timing: Timing is critical in the demolding process. The machine’s control system carefully monitors the curing time of the concrete mixture to ensure that the blocks are demolded at the right moment. Demolding too early can result in deformation, while demolding too late can cause the blocks to adhere to the molds.
- Controlled Ejection: Some concrete block making machines are equipped with ejectors or pushers that assist in the demolding process. These mechanisms gently push the blocks out of the molds once they are released, minimizing the risk of damage.
- Operator Monitoring: Operators play a crucial role in monitoring the demolding process. They visually inspect the blocks as they are demolded to ensure that they are intact and free from defects. Any blocks that show signs of damage or sticking may require adjustments to the demolding parameters.
By incorporating these techniques and technologies, concrete blocks machine can effectively manage the demolding process without damaging the freshly formed blocks, ensuring high-quality output and minimizing waste.
How does the cinder block making machine handle changes in production speed or output?
Cinder block making machines are designed to handle changes in production speed or output by employing several key mechanisms and strategies:
- Adjustable Settings: Many modern concrete blocks machines feature adjustable settings for parameters such as vibration frequency, compaction pressure, and material feed rate. Operators can modify these settings to accommodate changes in production speed or output requirements.
- Variable Frequency Drives (VFDs): VFDs are often used to control the speed of motors driving essential components such as the mixer, conveyor belts, and vibration system. By adjusting the frequency of the electrical supply to these motors, operators can vary the machine’s production speed to match changing demands.
- Multiple Mold Configurations: Cinder block making machines may be equipped with multiple mold configurations to produce different block sizes and shapes. Operators can switch between molds quickly to adjust production output according to demand.
- Automation and Control Systems: Advanced automation and control systems are integrated into many cinder block making machines, allowing for precise monitoring and adjustment of production parameters. These systems can automatically regulate processes such as material feed, compaction, and demolding to optimize production speed and output.
- Parallel Processing: Some cinder block making machines are designed to support parallel processing, where multiple tasks are performed simultaneously to increase overall efficiency and output. For example, while one set of molds is being filled and compacted, another set may be undergoing curing or demolding.
- Buffering and Storage Systems: Buffering and storage systems, such as pallet stacking racks or conveyor belts, are often incorporated into cinder block production lines. These systems allow for temporary storage of finished blocks, enabling continuous operation of the machine even during fluctuations in production speed or output.
- Monitoring and Optimization: Operators continuously monitor machine performance and production metrics to identify opportunities for optimization. By analyzing data on block quality, cycle times, and material usage, operators can make informed decisions to improve efficiency and maximize output.
- Scalability: Cinder block making machines are designed with scalability in mind, allowing for easy expansion or modification of production capacity as needed. cinder block making machine Additional modules or components can be added to the production line to accommodate increased demand without sacrificing efficiency or quality.
By incorporating these features and strategies, cinder block making machines can effectively handle changes in production speed or output while maintaining consistent block quality and maximizing efficiency.
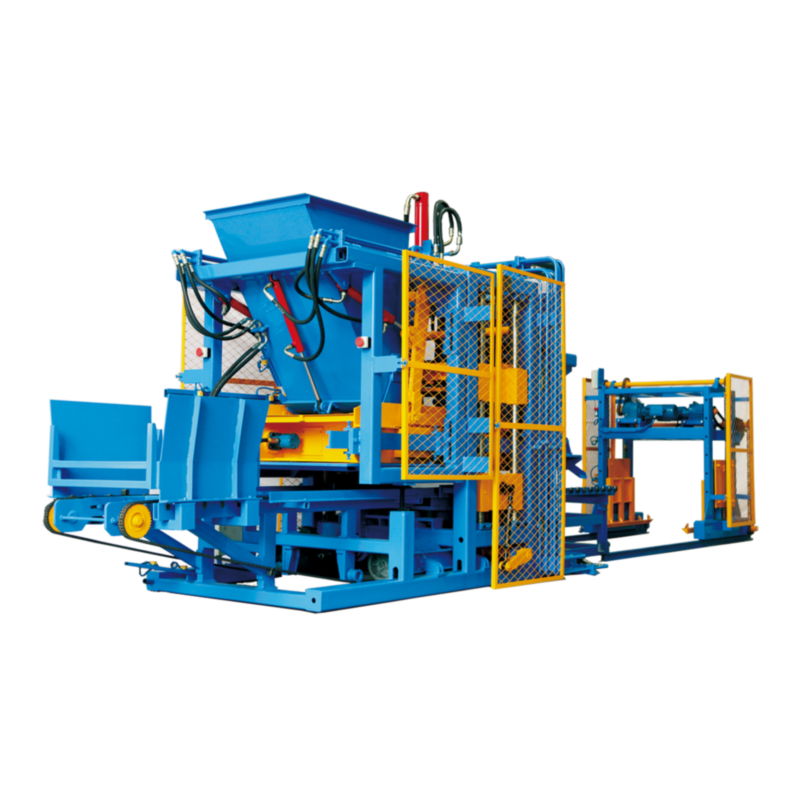