The energy consumption efficiency of a fiber laser marking machine can vary depending on several factors, including the power rating of the laser, the type of materials being marked, the marking speed, and the efficiency of the machine’s components.
Here are some considerations regarding the energy consumption efficiency of fiber laser marking machines:
- Laser Efficiency: Fiber lasers are known for their high energy efficiency compared to other types of lasers. They typically convert a higher percentage of input electrical energy into laser output energy, resulting in lower overall energy consumption for the same marking power output.
- Pulse Duration and Frequency: The pulse duration and frequency of the laser can impact energy consumption. Shorter pulse durations and higher pulse frequencies may result in more efficient material processing and lower energy consumption per mark.
- Marking Speed: Higher marking speeds generally result in more efficient energy usage since the laser spends less time interacting with the material. However, the optimal marking speed may vary depending on the material properties and desired marking quality.
- Material Compatibility: Some materials require higher laser power levels or longer processing times to achieve satisfactory marking results. Fiber Laser Marking Machine manufacturers Using appropriate laser parameters for each material can help optimize energy consumption efficiency.
- Idle Power Consumption: When the laser marking machine is not actively marking, it may still consume a certain amount of energy for system maintenance, cooling, and standby operation. Minimizing idle power consumption through efficient standby modes or power management features can improve overall energy efficiency.
- System Design and Components: The design and quality of components such as power supplies, cooling systems, and optics can impact the energy efficiency of the laser marking machine. Well-designed systems with high-quality components tend to have better energy consumption efficiency and overall performance.
- Environmental Factors: Ambient temperature and humidity levels can affect the energy consumption efficiency of laser marking machines, particularly cooling systems. Operating the machine within recommended environmental conditions can help optimize energy usage.
Overall, fiber laser marking machines are known for their energy efficiency compared to other marking technologies, but the specific energy consumption efficiency can vary depending on various factors. Optimizing laser parameters, system design, and operating conditions can help maximize energy efficiency while maintaining high-quality marking results.
How does it handle piercing of materials at different thicknesses?
Fiber laser cutting machines handle the piercing of materials at different thicknesses through a controlled process that considers factors such as material type, thickness, and cutting parameters. Here’s how they typically handle piercing:
- Pre-Piercing: For thicker materials, especially metals, fiber laser cutting machines often use a pre-piercing or pilot hole strategy. This involves first creating a small hole or indentation at the starting point of the cut path. The laser beam is focused at high power and intensity to melt or vaporize the material, creating an entry point for the subsequent cutting process.
- Piercing Parameters: The piercing process involves specific laser parameters such as power, pulse duration, and frequency tailored to the material type and thickness. The machine operator or control software sets these parameters based on material properties and cutting requirements. For thicker materials, higher power and longer pulse durations may be necessary to effectively pierce through the material.
- Assist Gas: Assist gases such as oxygen, nitrogen, or air are often used during the piercing process to help clear molten material from the piercing point and improve cutting quality. The choice of assist gas depends on the material being cut and desired cutting characteristics. Oxygen is commonly used for steel, while nitrogen is preferred for stainless steel and aluminum.
- Pierce Detection: Some advanced fiber laser cutting machines feature pierce detection systems that monitor the piercing process in real time. Fiber Laser Marking Machine suppliers These systems may adjust laser parameters or assist gas flow based on feedback from sensors to optimize piercing performance and ensure consistent quality.
- Adaptive Control: Certain fiber laser cutting machines employ adaptive control algorithms that dynamically adjust piercing parameters based on feedback from the cutting process. These algorithms may optimize parameters such as power, frequency, and assist gas pressure to account for variations in material thickness and composition, improving piercing efficiency and quality.
Overall, fiber laser cutting machines handle piercing of materials at different thicknesses by employing precise control of laser parameters, assist gas flow, and cutting strategies tailored to the specific material and cutting requirements. Advanced features such as pierce detection and adaptive control further enhance piercing performance and ensure consistent, high-quality cuts across a range of material thicknesses.
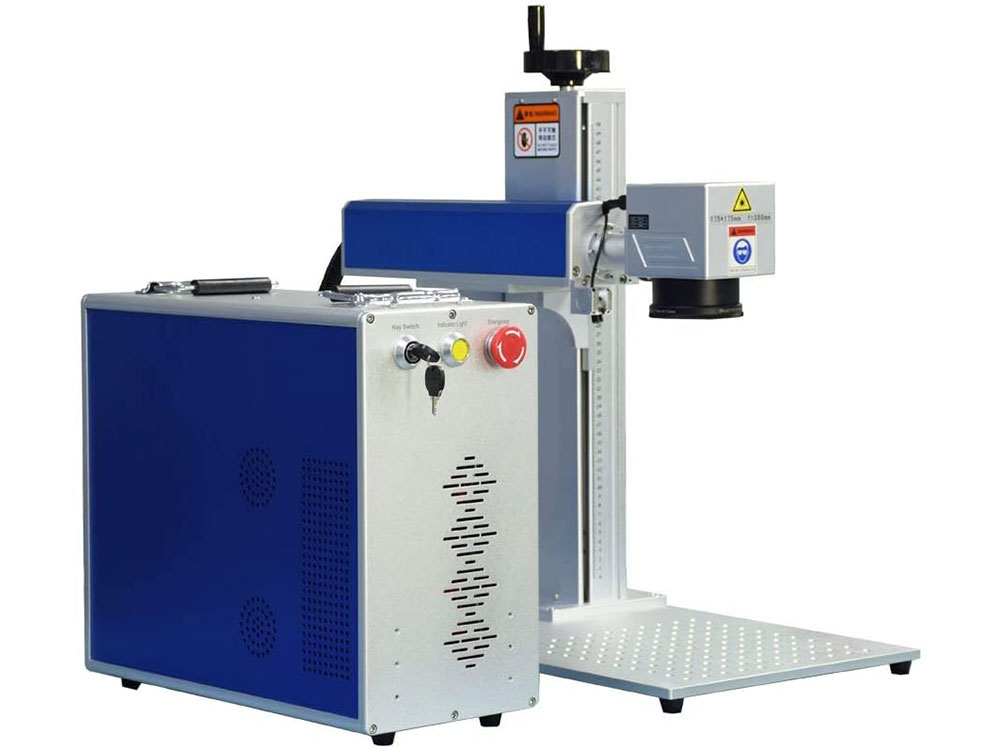